Polished concrete is a sustainable investment in your home
We have specialised in decorative polished cement coverings for more than 20 years, with over 2,000 realisations to our credit. These realisations span a variety of locations including restaurants, shops and exhibition spaces. We also work in private homes, applying our coating to kitchens, living rooms, dining rooms, stair cases, wall surfaces and bathrooms.
We use only high-strength mineral mortars that we also manufacture.
Our polished cement is a decorative interior coating based on cemented resin, intended for floors and walls. The shades are obtained by the addition of synthetic pigments or iron oxides. In particular, the coating consists of a thin layer of 1 to 3 mm, on any type of support — floors, new walls, and even in renovation directly on existing tiles.
Our products are absolutely unique and result in a smooth, structured surface with an unrivalled level of finish.
Nature of compatible media.
Our cement mortars used for polished concrete coatings can be applied to different surfaces such as cement or anhydrite surfaces, old tiles, as well as to concrete and other perfectly stable and rigid derivatives such as plasterboard, alba, wood, metal or others.
However, the substrates must be stable, dry and free of dirt. It is important to focus particular attention on these features to ensure the durability of the polished concrete coating and to avoid the appearance of cracks.
New or existing surfaces:
The high-strength mineral mortar is compatible with all types of surfaces. However, these must comply with SIA V567-251 and special attention must be paid to SIA V567-251 - 2.4, 2.46 and 2.47. — 5.7 to 5.74.
Existing tiles
When applying to tiles, they must be stable, firmly glued and must not have any cracks.
In the event of cracks, they must be investigated. Indeed, they often come from poor workmanship during implementation. In this case, a survey is necessary to check their hold and to detect any cracks that need to be sealed with epoxy resin.
Wooden floors and parquet - Dry surfaces:
Wooden floors and parquet floors are generally not compatible with polished concrete. Indeed, the instability of a wooden surface due to variations in humidity and temperature can cause micro-cracks in the cladding. However, in the case of use with moisture-resistant hydrophobic or phenol wood, the coating can be applied after certain specific preparations are carried out on furniture, kitchen countertops and washbasin shelves.
- For the floor: our system is compatible with dry surfaces such as Fermacell or Knauf. It should be noted that the sealing of the plates with a adhesive mortar reinforced with synthetic resins must be used and applied with great rigor. The joints between the panels are covered with a high-strength mortar.
- For walls: our system is compatible with Fermacell/Knauf panels, resin boards, plaster, various metals, etc. For wall surfaces, our coating is fully compatible with any stable substrate, subject to specific preparations.
The different stages of the installation of the polished concrete coating:
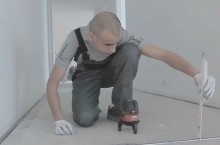
Renovation work
preparation :
Implementation of a substrate-specific adhesion primer. Installation of finishing or stop profiles according to request. Implementation of a self-levelling patching mortar in order to standardize the support.
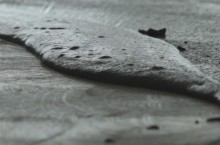
Primary mortar of polished concrete - P :
Application of a coat of adhesion primer.
Implementation of one or two layers of the primary mortar.
Sanding the primer.

Finishing mortar for polished concrete - F :
Application of one or two coats of finishing mortar depending on the desired appearance. Sanding and polishing of cement layers.
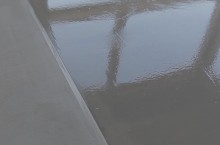
Protection of polished concrete for floor surfaces :
Application of a coat of varnish adhesion primer. Application of 2 coats of two-component matt varnish.
Timeline for the creation of a polished concrete surface :
A period of 5 to 7 days is required for the coating to be carried out. Between the preparation work and the different stages of construction including their drying times.
Flatness of the polished concrete coating :
The required surface quality can be within a level tolerance of plus or minus 4 millimetres for 1 metre of screed length.
Walkability of the floor and maintenance for varnished surfaces :
The floor is passable with care about 8 hours after the last coat of varnish. However, a period of five to seven days is necessary in order to obtain the final hardness of the varnish.
Care – Cleaning :
It is imperative to use suitable cleaning products with a neutral pH. Cleaning products based on soda, limescale removers or containing alcohol should be avoided to avoid damage to the protective varnish.
Tips Usage :
- Installation of protective pads under the legs of chairs and furniture.
- Office chairs: use of castors for parquet floors (equipped with a polyurethane strip, suitable for varnished surfaces).
Coating features observed over more than 15 years :
- In some cases, we have observed traces of stilettos.
- Beware of stagnant water. The installation of a floral arrangement in direct contact with the ground without a plant pot can leave traces in the covering.
Dominant qualities – Aptitude :
- The absence of seals makes it hygienic and very easy to maintain.
- Its density improves heat exchange for underfloor heating.
- Its implementation in several cross-layers promotes consistency of execution.
- Its varnished surface ensures exceptional comfort.
Our recommendations are based on tests and practical experience over several years. The data and results may be influenced depending on the conditions of implementation.
All details presented are given for information purposes only and do not represent a condition of responsibility.
These data cannot therefore be used as a basis for the assessment of reparations.